Painting Novacryl®
Discover the art of painting Novacryl®, where photopolymer signs come to life with a myriad of custom colors and designs. Whether surface painting or incorporating colors and patterns within the base substrate, a clear coat provides essential protection and should be applied with precision to ensure longevity and durability.
Applying Clear Coats and Paints to Photopolymer Signs
Many Nova photopolymer substrates provide you the opportunity for either first-surface or second-surface painting. Signs that are decorated subsurface with paint, digital graphics, and materials that incorporate color or patterns in the base substrate all require a clear coat to be applied over the photopolymer. Clear coating any Nova photopolymer sign provides the extra benefit of added protection against harsh cleaning and disinfectant chemicals and provides graffiti resistance.
According to Matthews Paint Company, it is specified that applying paint colors and/or clear coats should have the same amount of coating (4 mil wet/2 mil dry). Whatever paint system you use, ensure that mixing and application are according to the manufacturer’s instructions and recommendations.
It should be noted that when using either paint colors or clear coats, be sure to use the lower gloss level appropriate for ADA compliance.
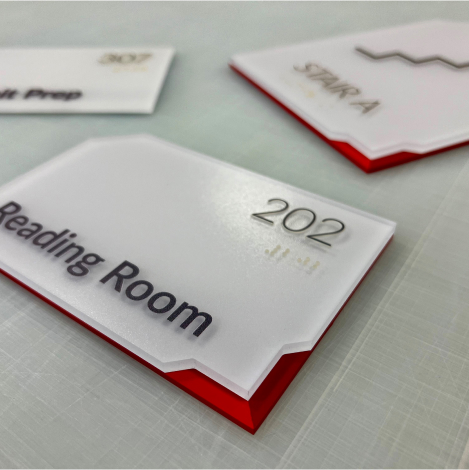
Recommended Procedures for Painting Novacryl
Prior to painting or clear coating any Novacryl® substrate, the first step with any paint prior to painting is to clear the polymer substrate. This can be accomplished with a quick blast of compressed air. You will want to ensure that the substrate is dry prior to any paint preparation. You may use any of our reducers or isopropyl alcohol.
Paints used in the sign industry all have their recommendations for clearing and application of either a primer coat or a direct application of paint colors or a clear coat. Matthews Paint, as an example, provides the sign painter with a complete substrate guide, which includes Nova substrate recommendations. Nova Polymers substrates can have paint colors or clear coats applied directly. Nova’s polymer substrate, after processing, provides a surface that is very paint color or clear coat receptive. However, if the applicator wishes to use an adhesion promoter prior to color or clear coat application, always follow the manufacturer’s product and application recommendations. As in the case of Matthews Paint, they recommend the use of Tie Bond (74-777SP or 274-777SP) in this adhesion promoter for Nova Polymers when desired.
When using VOC-compliant MAP, our compliant coating for air regulations, be sure the photopolymer is clean. Then, apply our VOC-compliant material directly to the photopolymer. No Tie Bond is necessary for good adhesion.
The top coating of MAP and VOC MAP should be done within 72 hours. After 72 hours, a light scuff sanding with 400 grit sandpaper is required for good adhesion of any top coating.
Complete Matthews Paint Company Substrate Guide
Substrate Preparation Recommendations
Step 1
Matthews is for professional use only.
Step 2
Always follow proper safety precautions when using Matthews’s products.
Safe usage requires reading, understanding, and following all labels, SDS, and other product literature before use.
Step 3
The spray area and substrate must be warm and have adequate airflow.
Application of primers, topcoats, and clear coats should never take place in temperatures under 60F/16C. Substrates should also be brought to or above this temperature guideline before applying any primer or topcoat.
Step 4
Properly clean the substrate.
Professionals don’t even think about priming or painting over any substrate that hasn’t been properly cleaned and prepared. Use proper cleaning products and procedures.
Step 5
Use the right primer for every specific substrate.
Always use the appropriate primer and application techniques suggested by Matthews’ substrate guide.
Step 6
“When in doubt, test it out.”
Recommend testing first, the process for any new product, primer, or first-time application procedures before permanent production begins. Remember that the change of seasons affects the temperature and humidity during application, so periodic testing on application and adhesion confirms the product and production performance.
Step 7
Choose the proper reducer for each application.
Review product data sheet for reducer temperature guidance.
Step 8
Allow specific time between coats.
For both primers, topcoats and clears, extend flash times between each coat application.
Step 9
Adjust spray equipment.
Perform a spray pattern check prior to painting. Adjust flow, pressure, and tip if necessary. Use in well-ventilated facilities and with proper safety equipment.
Step 10
Contact Matthews Paint Company with any questions.
Matthews’s customer service and technical assistance are both available for any color formula match, specification, or technical question that may arise.
How Do I Use a Wet Film Thickness (WFT) Gauge?
A wet film thickness gauge is designed to give the spray operator immediate feedback as to the film builds just sprayed. In most cases, measuring the dry film thickness (DFT) provides little information as it is usually measured a considerable amount of time after the actual spraying. Many things could have influenced the DFT: operator fatigue, ambient air temperature, coating temperature, etc.
There are several types of WFT gauges available, the most common being the notch gauge. Other types, including the eccentric disk, the rolling notch gauge, and the 6-sided gauges, are available from specialty vendors.
There are several issues that must be addressed when using a WFT gauge
- 1.Technique
- 2. Timing
- 3. Reading with clear coats
- 4. Creating surface defects
Technique
When placing the gauge on a freshly painted part, the gauge must be placed 90 degrees to the part. The operator also needs to be aware of the variation of the surface that may influence the reading. For example, if the surface is not perfectly flat, one direction may give a more accurate reading than another.
To use the WFT gauge, place the gauge directly on the wet finished part and as described above. The notches will indicate the measured film thickness. For example, if the 1 and 2 mil notches are wet and the 3 and 4 notches are dry, then the measured thickness is between 2 and 3 mils (.002 to .003 inches).
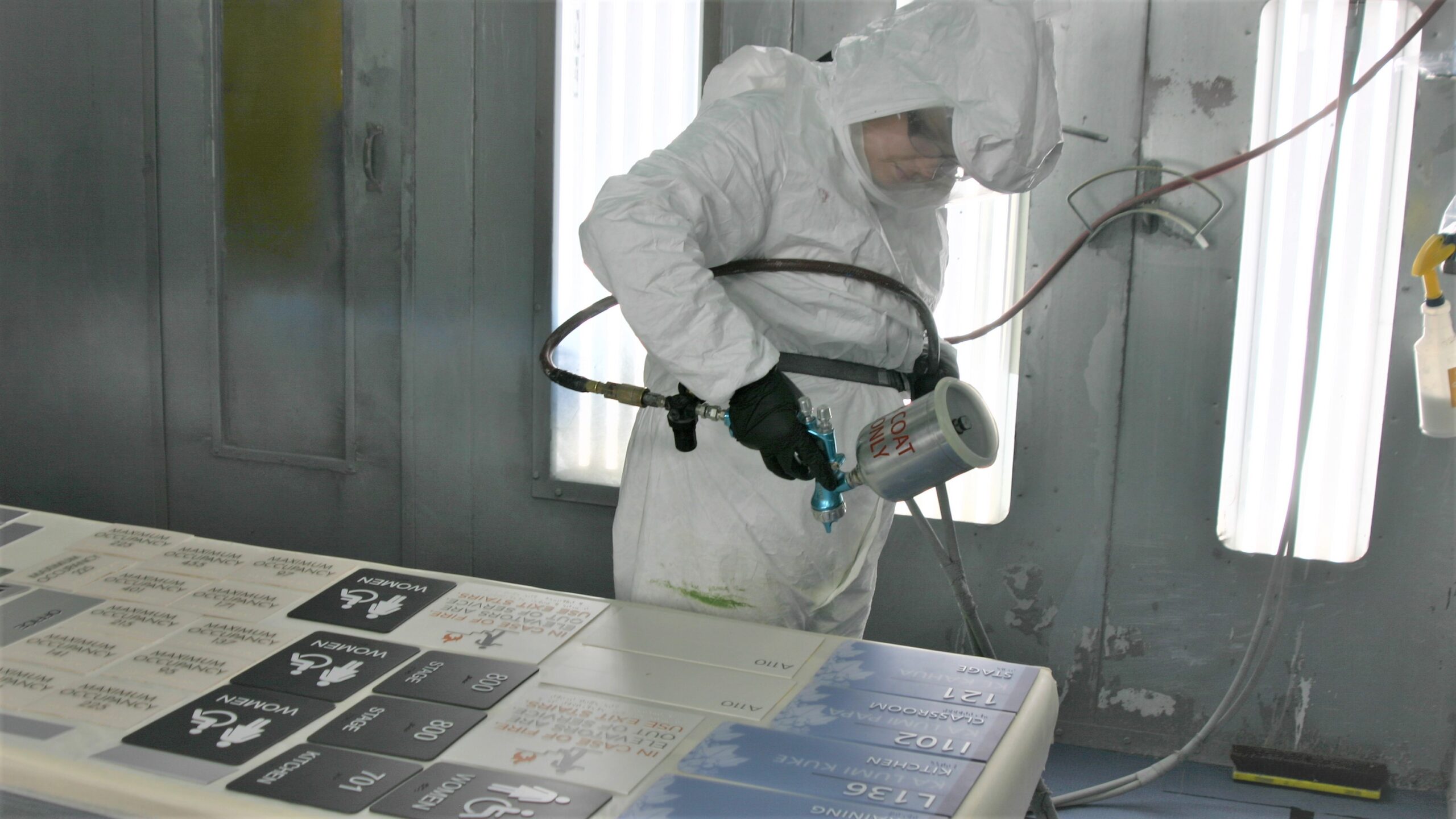
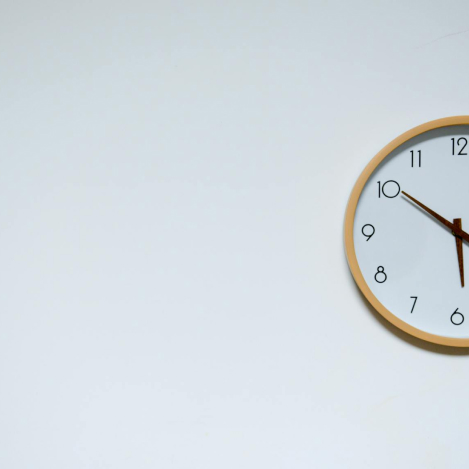
Timing
The solvent in a coating will immediately start to evaporate after spraying. In order to achieve a common method of reading the coating thickness, a time frame will need to be established. Typically, one might measure the thickness of 5 to 10 seconds after spraying. If another operator measures the thickness after 20 seconds, the results would be different even if the initial thickness was identical.
Reading with Clear Coats
A clear coating on a WFT gauge would be very difficult to read. The most common method of reading clear coats is to use the gauge as a stamp on a piece of absorbent (non-gloss) paper. Many companies use the stamp method as a way of documenting the WFT.
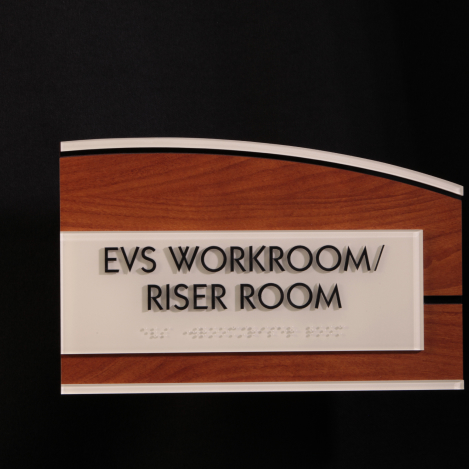
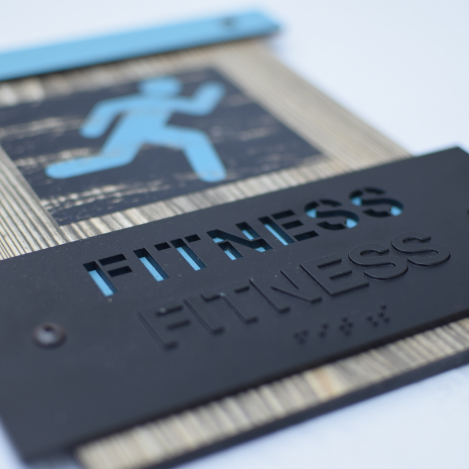
Creating Surface Defects
After using a WFT gauge to check the film thickness, the material may not flow to hide the area where the gauge was used. If this creates an undesirable defect, place a small sample of the material in line with the operator’s normal spray path. This sample should be sprayed along with the part. The sample then may be checked for WFT and DFT (after curing).
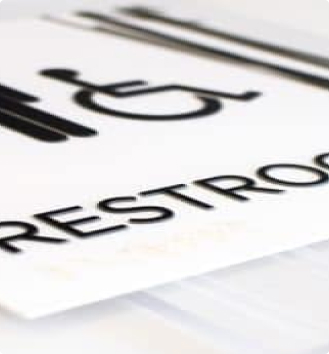
Recommendations for Maintenance Cleaning of Novacryl Completed Signs After Installation
- 1. It is recommended to wait at least 30 days after painting before any cleaning or polishing is attempted
- 2. The maintenance and care of a painted or clear-coated polyurethane surface would utilize the basic commercially available non-abrasive cleaners and polishes recommended for finishes exposed to the environment.
- 3. A mild detergent and water solution with soft cloth toweling is often sufficient to remove most dirt, followed by a thoroughly clean water rinse. Never scrub, abrade, or use powdered cleansers for cleaning. Simple over-the-counter soaps or disinfecting agents work best.
- 4. Any questions should be directed to the manufacturer’s recommendations